NORTH RIDGEVILLE, Ohio — From Cleveland to Columbus and Toledo to Cincinnati, Ohio is packed with companies who call the Buckeye State home.
As part of the News 5 Cleveland Buckeye Built series, reporter Meg Shaw went behind the scenes to see how football helmets are made by hand at Riddell.
History
The Riddell company was first started in 1929 by John Tate Riddell. He first came into the game by developing a removable football cleat. Riddell wanted to make the game of football safer for athletes all over the country.
But it was in 1939 when his main invention took center stage. It was the year when he created the first-ever plastic football helmet shell.
Over the years, of course, this invention has taken on many upgrades. Throughout the 40s, 50s, 60s and 70s, many additions were made for the helmet shell, including the chin strap, face mask, nose protection and more.
In 2002, the company created the Riddell Revolution. It was the first helmet made in 25 years that was aimed at reducing concussions.
Since then, the technology inside the helmets continues to improve as the company utilizes data and lab studies showing impact to a player's head.
Made in Ohio
Riddell employees have been making helmets in the Buckeye State by hand since the 90s. For several years, the Riddell manufacturing plant was based on Sugar Lane in Elyria. The 220,000-square-foot plant housed a couple hundred employees.
For years, hundreds and thousands of helmets were hand-produced at the Sugar Lane facility. But in 2016, the company announced operations would be moving.
"We were really only looking within a 12 to 20 mile radius for a new location," said Riddell's manufacturing general manager, Ben Marker. "Because we wanted to make sure that we retained each and every one of those employees."
Fortunately, the move didn't even span 10 miles.
Riddell built a new 350,000-square-foot facility two miles down the road, off of Center Ridge Road in North Ridgeville.
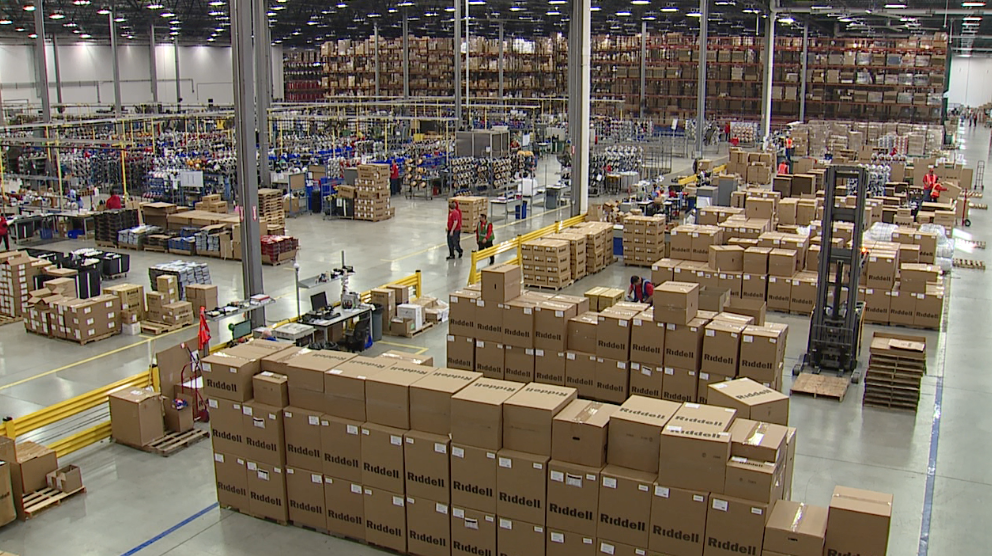
"A football helmet is highly configurable," Marker said. "There's just a lot to it and there's a lot of knowledge that an employee needs to have. So it was important for us to stay very local - to move very local from where we're coming from. So their experience was highly valuable to us. Starting someplace brand new with a full line of new employees would have been extremely challenging, just based on the complexities of our market."
Marker walked our camera crew through the manufacturing facility floor, showing how each and every helmet is made by hand.
"You need a set of hands and a set of eyes on almost every single helmet to ensure that it's built properly and then it meets customer specifications," he said.
He said every helmet goes through at least 10 to 12 inspection points before it goes out as a fully formed piece of equipment.
Erin Griffin, the vice president of Riddell's marketing, said Northeast Ohio employees have played an inaugural part in the company's success inside the U.S. and out.
"The workforce here in North Ridgeville, Ohio has the opportunity to put their stamp of approval and their skilled work on football helmets that are going all over the US, Canada and even the world," Griffin said.
Helmet Safety
It's no secret helmet safety has been under fire for the last decade, leaving Riddell caught in the middle.
The company has faced a number of lawsuits from players and their families, claiming the the company's defective helmets have caused brain injuries.
Just recently, in October 2019, an appellate court of Illinois ruled that a group of more than 50 NFL players waited too long to sue the helmet maker. Court documents said, "the trial court found that, because the players had already sued the NFL more than two years before filing these cases, the players knew about their injuries and, therefore, could have sued the helmet manufacturers at the same time."
Griffin said at the end of the game, they want players to go home safely.
"Based at our core, we're working to improve player protection. And so we've always been focused on that effort and continuing to advance helmet technology, as the science has supported advancements and materials have become available and new techniques to designing and developing equipment," she said.
Griffin said for 15 years, Riddell has been collecting data from impacts on the field. Their scientists use the data they receive to make changes to their products to minimize the injury a player experiences during the game of football.
"We see data driving performance decisions, protection decisions, on field decisions, in terms of technique, player behavior, practice habits, all of those things are being evolved because of data. In addition, we're adjusting how we make our football helmets, we're creating new protective systems based on information coming from the football field. So as everything in life is tapping into data, football is no different," she said.
One of their newest helmets is now the third safest on the market, according to the NFL and National Football League Players Association.
The SpeedFlex Precision Diamond helmet has a 3D printed liner inside the helmet. The company paired up with Silicon Valley-based Carbon to put the helmet on the market.
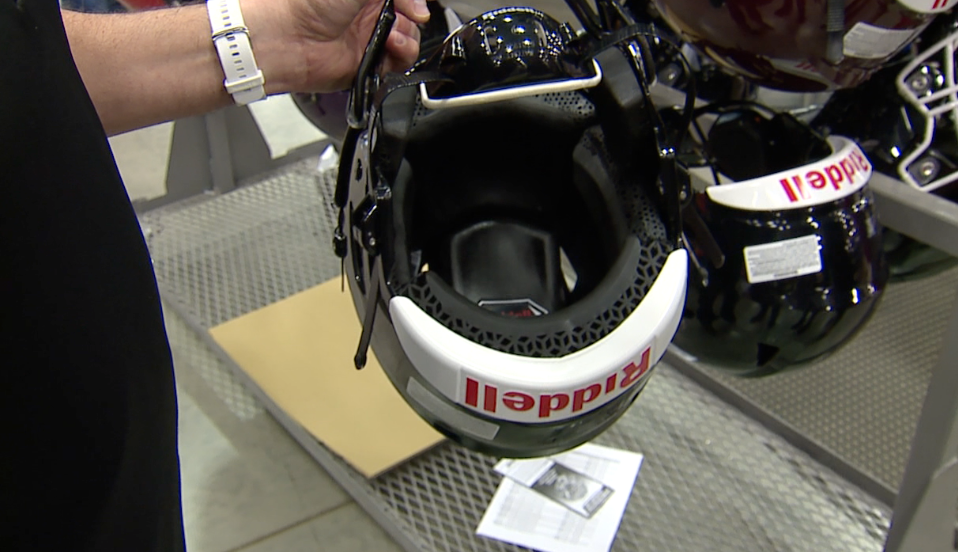
For the most part, only NFL players are wearing the 3D technology. But, Griffin said, in the 2020 football season, more colleges and high school teams will be wearing them during games.
Reconditioning
Riddell is the largest football helmet reconditioner in the world.
At the end of each season, helmets and other equipment are sent back to the North Ridgeville facility for reconditioning.
Marker said helmets are disassembled, buffed, sanded, sanitized, hand-inspected, repainted and tested before heading out the door for another season on the field.
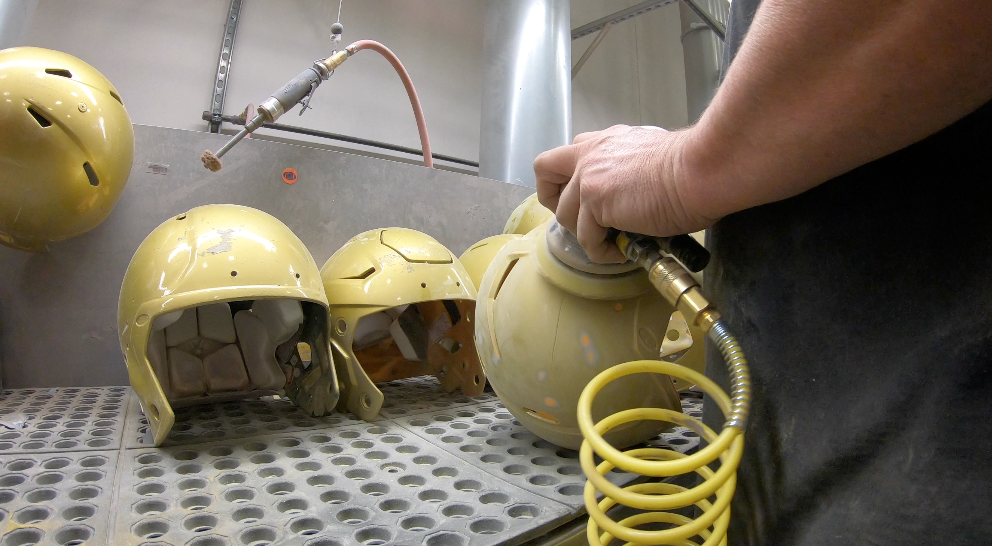
Helmets can be used for approximately 10 years and then they need to be discarded or removed from play.
"It helps with athletic departments, to allow them to reuse their helmet from year to year and then transition only a part of their inventory of helmets into new helmets," Griffin said.
For more information on Riddell, click here.